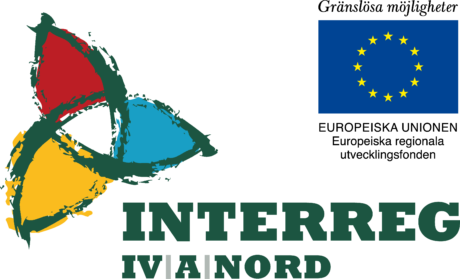


FATLASE – Fatigue durability of laser clad components
Companies benefiting the project include end users of laser coatings (large diesel engines, power transmission components, hydraulic cylinders, pulp and paper handling equipment) and laser cladding job shops.
Toimiala: Tuotantoteknologia
Projektin kesto: 01.01.2011 – 31.12.2012.
Toiminta-alue: Kansainvälinen
Rahoittajat: Interreg IV A North program, Regional Council of Lapland, KOSEK – Kokkolanseudun Kehitys Ltd., Länsstyrelsen Norrbotten and Finnish industry.
Budjetti: 450 000 EUR
Lisätiedot: Marko Forsell, RD manager, +358 40 8085128
Projektipäällikkö: Lasse Jansson
Background
Tampere University of Technology (TUT), Luleå University of Technology (LTU), Technology Centre KETEK Ltd. and CENTRIA research unit of the Central Ostrobothnia Polytechnic run the project concerning fatigue strength of laser clad components.
Project lasts 2 years covering the period of 1.1.2011-31.12.2012. Total budget of the project is 0.45 MEUR.
FATLASE research project is funded by EU’s Interreg IV A North program, Regional Council of Lapland, KOSEK – Kokkolanseudun Kehitys Ltd., Länsstyrelsen Norrbotten and Finnish industry. Companies benefiting the project include end users of laser coatings (large diesel engines, power transmission components, hydraulic cylinders, pulp and paper handling equipment) and laser cladding job shops. It is also meant for those who want their end products to be qualified and proved by official classification societies.
Laser cladding as an overlay welding method induces large residual stresses and moderate metallurgical changes in components, potentially affecting their behaviour under external stresses. Among the mechanical properties which affect the service life of the component, the most important one is the fatigue strength. Under alternating loads unpredictable cracks, which may lead to catastrophic failures, can initiate under stresses which are well below the ultimate tensile and or even yield strength limits of the material. It has been estimated that 70-90% of all the mechanical failures in machines and components are due to combined effects of different modes of fatigue (axial, torsion and bending). Representative examples are various power transmission components.
Metallurgical changes and residual stresses caused by laser cladding depend primarily on the materials involved. Frequently, laser clad components comprise a substrate of hardenable carbon, tool or quenched and tempered steels with a low coefficient of thermal expansion (CTE) and a coating of Fe, Ni or Co-based super- or hardfacing coating alloys with high CTE. In these situations, the coating layer is in tension, which is detrimental to fatigue strength and durability. A hardened heat affected zone (HAZ), in turn, decreases the overall ductility of the component. The HAZ can be, however, tempered during post-heat treatment, but tensile residual stresses in the coating layer cannot be totally eliminated if CTEcoating > CTEsubstrate. The residual stress state is also influenced by post-machining, which is frequently practiced on laser coatings. Occasionally, internal cladding defects such as inter-run, solidification or gas pores occur. These structural discontinuities may act as initiation sites for fatigue cracks due to the localized stress peaks they create. For these reasons and due to the lack of available data on fatigue strengths of laser clad components, there is considerable practical and scientific interest in a comprehensive and systematic fatigue analysis relevant to this process.
The main objective of the project is an increase in knowledge concerning the applicability of laser clad components in conditions where they are subjected to fluctuating stresses. This involves an investigation into the influence of laser cladding on a components’ fatigue durability under axial, torsion and bending loads. This will be achieved by conducting large scale low- and high-cycle laboratory fatigue tests on laser clad components, and comparing the results to those of the substrate materials alone and laser clad and post-heat treated components. Extensive test programs will be carried out using testing devices equipped with closed-loop servohydraulics, which produce exceptionally high dynamic loads in order to use large test pieces which replicate real industrial components, where coating/substrate and HAZ/substrate thick-ness ratios are low. In order to explain the experimental results and deepen the understanding concerning the stress formation and crack initiation during fatigue, simulation and modelling will be carried out using finite-element (FE) analysis. Since there is lack of data regarding fatigue performance of laser clad components in the literature, the results obtained in the project will have a substantial scientific impact on the field and be a significant contribution to laser materials processing research. Besides the direct scientific objectives, one essential goal of this project is to initiate solid and close collaboration between two leading laser materials processing research units (Kokkola-Luleå) in the field of surface treatments in Nordic region.
Contact Information
Prof. Petri Vuoristo, TUT
petri.vuoristo@tut.fi
+358 (0) 40 849 0044
Jari Tuominen, TUT
jari.tuominen@tut.fi
+358 (0) 40 849 0196
Prof. Alexander Kaplan, LTU
Alexander.Kaplan@ltu.se
+46 (0) 920 491 733
Tuomo Peltola, KETEK
tuomo.peltola@ketek.fi
+358 (0) 44 725 0201
Lasse Jansson, CENTRIA
lasse.jansson@centria.fi
+358 (0)44 725 0072